برخی از فنهای گریز از مرکز در کاربردهای صنعتی در محیطهای ساینده قرار دارند. پس از گذشت مدت زمانی کار کردن، سطوح ساییده شده این فنها نیاز به تعمیر یا تعویض دارند. در برنامهریزی و انجام تعمیرات جوشکاری بر روی این سطوح ساییده شده، چندین نکته مهم وجود دارد. ابتدا، باید سایش شناسایی و کمیتگذاری شود و تخمینی از عمر مفید باقیمانده سطوح ساییده شده تهیه شود. سپس، دامنه و نوع تعمیرات باید مشخص شود. در نهایت، یک برنامه تعمیر جامع باید تهیه شود و یک تکنیک تعمیر پیش از شروع کار توسعه یابد. این مقاله به بررسی روشهای عملی برای انجام این مراحل به سمت یک تعمیر موفق میپردازد.
الگوهای سایش
در برخی مواقع، شناسایی الگوهای سایش و کمیتگذاری میزان از دست رفتن ماده کار دشواری نیست. با این حال، بیشتر اوقات، نیاز به کمی کار شناسایی، آزمایش و ترندینگ سایش(بررسی و پایش روند سایش) است تا اطلاعات مفیدی به دست آید.
برای هر تلاشی در زمینه ترندینگ سایش، لازم است یک خط پایه تعیین شود تا معنیدار باشد. این کار بهراحتی هنگامی انجام میشود که تجهیزات جدید باشند. اکثر تولیدکنندگان فنها، نقشهای از ایمپلر فن ارائه میدهند که ابعاد کلی، نوع مواد و ضخامت اجزا را نشان میدهد. حتی اگر چنین اطلاعاتی از سازنده اولیه در دسترس نباشد یا اگر تجهیزات سالها در خدمت بوده باشند، هنوز هم میتوان شرایط خط پایه را تعیین کرده و سایش تجربه شده توسط فن را ترند کرد.
الگوهای سایش بهطور گستردهای متغیر هستند، حتی در فنهای چپ و راستی که همزمان و در کنار هم بر روی یک سیستم در سرویس هستند؛ زیرا الگوی سایش میتواند تحت تأثیر عواملی مانند پیکربندی داکت، تنظیمات دمپر و توزیع گرد و غبار در داکت قبل از فن قرار گیرد که همه اینها پارامترهای بیرونی از فن هستند. در شکل 1، چند الگوی سایش معمولی قابل مشاهده است. مشاهده بصری الگوهای سایش ثبتشده با ترسیمها یکی از مفیدترین سوابق تاریخ سایش است. ضخامتها میتوانند با خطکش، کالیپر یا گیجهای ضخامتسنجی فراصوت اندازهگیری شوند. در مناطقی که سایش قابل توجهی مشاهده میشود، ترند کردن نرخ سایش به پیشبینی عمر مفید سطح سایش کمک میکند. این موضوع بهویژه زمانی مهم است که سطح سایش یکی از اجزای سازنده ایمپلر فن باشد.
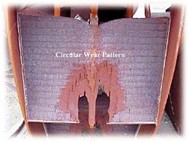
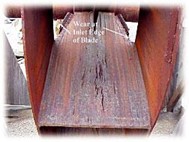
شکل 1
ترندینگ، مانند آنچه در شکل 2 نشان داده شده، پیشبینیهای عمر باقیمانده را امکانپذیر میکند و برنامهریزی تعمیرات یا تعویضها را تسهیل میسازد. ترندهای سایش که شامل از دست دادن مواد از اجزای سازنده نیستند، معمولاً میتوانند با قضاوت مهندسی مدیریت شوند. مثلا اگر یک صفحه سایش در ابتدا 6mm ضخامت داشته و در بدترین ناحیه سایش 1.5mm در سال ماده از دست میدهد، باید در سال سوم قبل از اینکه سایش بر ساختار زیرین تأثیر بگذارد، تعویض شود. پیشبینی عمر زمانی دشوارتر میشود که مواد از ساختار ایمپلر فن از دست برود، زیرا این امر میتواند بر یکپارچگی سازهای فن تأثیر بگذارد. زمانی که خسارات سایش پیشبینی شده شامل اجزای سازنده باشد باید با یک طراح فن با تجربه مشورت شود.
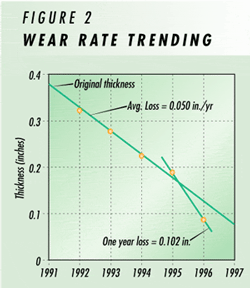
شکل2
تعیین نوع تعمیر
نوع تعمیر مورد نیاز معمولاً با توجه به میزان سایش فن مشخص میشود. سادهترین تعمیرات شامل انباشته کردن جزئی سطوح سایش، چه در قسمت سازنده ایمپلر فن و چه در یک جزء مقاوم در برابر سایش، مانند صفحه سایش، است که قسمت سازنده ایمپلر را محافظت میکند. در تئوری، تا زمانی که فلز پرکننده مورد استفاده برای تعمیرات از نظر استحکام، سختی و چقرمگی با فلزی که جایگزین میکند، قابل مقایسه باشد، میتوان تعمیرات وسیعی بر روی اجزای ایمپلر انجام داد. از نظر عملی، چندین عامل وجود دارد که دامنه تعمیراتی را که باید در محل انجام شود، محدود میکند.
اول، جلوگیری از تاب برداشتن در اجزای ایمپلر که تعمیرات وسیع با جوشکاری انجام شدهاند، دشوار است. تغییرات هندسی نامطلوب میتوانند منجر به ساییدگی، کاهش عملکرد و افزایش پتانسیل سایش شوند.
دوم، کنترل دقیق مقدار و محل فلز جوش داده شده در حین تعمیرات بسیار دشوار است، که تقریباً همیشه منجر به لرزش قابل توجهی در هنگام راهاندازی مجدد فن میشود.
سوم، زمان مورد نیاز برای جوشکاری وسیع معمولاً در دسترس نیست و این امر گزینههای دیگر را جذابتر میکند.
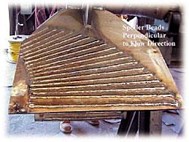
شکل 3
نوع دیگری از تعمیرات ساده، hardfacing (شکل 3) است. رایجترین عمل این است که از فلز پرکنندهای استفاده شود که به طور قابل توجهی سختتر از ماده سازنده ایمپلر است. این دانهها به صورت عمود بر جهت جریان محلی قرار میگیرند تا جریان گرد و غبار را از سطح ایمپلر بلند کنند. این دانهها در مناطقی اعمال میشوند که به یک صفحه سایش کامل نیاز ندارند، اما به اندازه کافی سایش دارند که به اجزای سازنده آسیب برسانند.
همچنین میتوان صفحات سایش یا بخشهایی از آنها را در محل تعویض کرد. صفحات سایش با اندازهها و مواد مختلف اغلب به نواحی آسیبپذیر فن اضافه میشوند تا از آسیب به اجزای زیرین محافظت کنند. در اینجا نیز تصمیم گیریهای فنی است که باید تعیین کند که چه مقدار باید تعویض شود. اگر بخشی کوچک از یک صفحه سایش کامل، به اندازهای ماده از دست داده باشد که ساختار زیرین را نمایان کند، اما باقیمانده صفحه بتواند چندین سال دیگر با نرخ سایش فعلی عمل کند، تنها باید همان بخش کوچک تعویض شود. باید دقت شود تا قسمت تعویضشده به خوبی با باقیمانده سطح سایش ترکیب شود، زیرا لبههای بیرونزده تمایل دارند سریعتر از نواحی اطراف سایش پیدا کنند. همچنین میتوان صفحات سایش کامل را در محل تعویض کرد. WPSهای تهیه شده جهت جوشکاری باید به دقت دنبال شوند.
موادی که برای این صفحات سایش استفاده میشوند معمولاً در یکی از سه دسته زیر قرار میگیرند:
- آلیاژی مشابه یا یکسان با آلیاژهای مورد استفاده در اجزای سازنده
- فولادهای کویینچ و تمپر شده
- مواد کامپوزیتی با سطح سخت و مقاوم در برابر سایش که بر روی یک سطح دیگر که جوشپذیر است و یا با اتصال پیچی قابل بستن است اعمال میشود.
متریالهای کوییننچ و تمپر شده در انواع مختلف آلیاژها و سختیها موجود هستند. بیشتر آنها در دسته فولادهای کم آلیاژ قرار میگیرند و بسیاری از آنها به عنوان آلیاژهای اختصاصی در نظر گرفته میشوند، یعنی بر اساس مجموعهای شناختهشده از مشخصات مانند ASTM تولید نمیشوند. سختی این آلیاژها از حدود 300 تا 600 BHN متغیر است. بهطور کلی، هرچه سختی بیشتر باشد، دشواری جوشکاری نیز بیشتر خواهد بود. برای مثال ورقهای HARDOX و QUARD که با سختیهای متفاوتی تولید میشند را میتوان نام برد.
مواد کامپوزیتی (بی متال) که بسیار گسترده هستند و میتواند شامل یک لایه جوش بر روی فولاد کربنی با کربن کم و منگنز متوسط باشد و یا یک پوشش نازک کاربید تنگستن که به طور کورهای بر روی یک فلز پایه جوشپذیر متصل شده است. یکی از رایجترین مواد کامپوزیتی که امروزه استفاده میشود، ترکیب جوش کاربید کروم بر روی یک ماده پایه فولاد سازنده است.
یک استراتژی دیگر برای مقاومت در برابر سایش، جوش دادن فلز سختکننده (HARDFACING) به طور مستقیم به اجزای سازنده فن در ناحیه آسیبدیده است. این استراتژی زمانبر است و معمولاً فقط به طور محدود اعمال میشود.
پوششهای اسپری حرارتی یک دسته دیگر از استراتژیهای مقاوم در برابر سایش را ارائه میدهند. تقریباً هر فلز پرکنندهای که بتوان آن را جوش داد، میتواند بر روی یک سطح اسپری شود. برخی از روشهای اسپری اجازه استفاده از سرامیکها و سایر مواد غیرجوشپذیر را نیز میدهند.
تعمیرات ترکیبی
استفاده همزمان از چند استراتژی در برخی از کاربردها غیرمعمول نیست. برای مثال، یک تیغه فن ممکن است در نواحی با بالاترین سایش با یک کامپوزیت پوششدار کاربید کروم محافظت شود، در نواحی اطراف آن از ورق کویینچ و تمپر شده استفاده کرد و حاشیه پره ها را نیز به روش HARDFACING جوشکاری کرد.
اگر آسیب خیلی گسترده نباشد، بخشهایی از ساختار ایمپلر میتوانند در محل تعویض شوند. این نوع تعمیرات نیاز به برنامهریزی و بررسی دقیق دشواری جوشکاری فلزات سازنده دارند. معمولاً تعویض اجزای ایمپلر با تعمیر یا تعویض سطوح سایش ترکیب میشود. این نوع تعمیرات ترکیبی از همه پیچیدهتر است.
هشدارهایی که با هر یک از استراتژیهای تعمیر فوقالذکر همراه است، شامل نگرانیها در مورد افزایش اینرسی چرخش است که با هر افزودن ماده به یک مجموعه چرخان همراه است، نگرانیهای مربوط به افزایش هزینههای اولیه و نگرانیها درباره کاهش یکپارچگی سازهای، یکی دیگر از نگرانیهای مهم به حساب می آید.
اجراي تعمیر
بر اساس پیشبینی عمر سایش، ممکن است تمهیداتی در سیستم مقاوم در برابر سایش علاوه بر تعمیرات لازم باشد. نتیجه این مرحله یک طراحی نهایی بهبود یافته خواهد بود. طراحی باید شامل هندسه نهایی که در تعمیر بهدست خواهد آمد و مواد مورد استفاده برای سطوح سایش و جوش باشد. حتی برای تعمیرات ساده، باید یک دستورالعمل تهیه شود تا جوشکاران و بهره برداران، طراحی نهایی را ببینند و جزئیات مرحله به مرحله فرآیند تعمیر را به درستی درک کنند.
تمام مواد جوش شونده در فرآیند تعمیر باید شناسایی شوند، حتی اگر تنها در مجاورت ناحیه تعمیر باشند، و باید یک مشخصه کامل برای روش جوشکاری (WPS) برای اتصالات جوش توسعه یابد. روشهای جوشکاری باید بر اساس AWS D14.6 تأیید شوند. متأسفانه، به دلیل سختی و تردی شدید بسیاری از مواد مقاوم در برابر سایش، امکان قبولی در آزمونهای خم و کشش مورد نیاز برای دریافت WPS کاملاً تأییدشده وجود ندارد. مواد مصرفی جوشکاری و جوشکاران نیز میتواند تحت AWS D14.6 تأیید شود.
به عنوان بخشی از طرح تعمیر، باید به حذف مواد سایش یافته و برخی جوشهای موجود و سایر رسوبات مقاوم در برابر سایش توجه شود. حذف صفحات سایش نسبتاً ساده است و کمی سنبادهزنی در نواحی ساییدهشده قبل از جوشکاری کردن میتواند سطح را بهطور معقولی آماده کند. با این حال، باید توجه ویژهای به جوشکاری سطوح سخت قبلی داشت، چرا که معمولا خواص جوشپذیری خوبی ندارند. از آنجا که مکانیزم اصلی مقاومت در برابر سایش در بیشتر سیستمهای سایش فن، سختی بالا است، ترکیب شیمیایی جوشهای سطح سختشده قبلی با فلز جوش سازنده بسیار متفاوت است. حتی مقادیر جزئی از رقیقسازی جوش سطح سختشده در فلز جوش سازنده میتواند نتایج فاجعهآمیزی به همراه داشته باشد.
پس از تکمیل تمامی برنامهها، تیم تعمیر باید گرد هم آمده و کل طرح را مورد بحث قرار دهند. هر مرحله اصلی برنامه باید توضیح داده شود، بازخورد گرفته شود و لیستی از مواد و تجهیزات مورد نیاز برای کار تهیه گردد. روشهای مناسب آزمایش غیرمخرب نیز باید در برنامه کار گنجانده شوند و یک بررسی کیفیت مستقل پس از اتمام پروژه انجام شود.
برای نشان دادن اصول و ایدههای مطرح شده در بالا، یک برنامه تعمیر نمونه در زیر آورده شده است. هدف این طرحی که در این مثال مورد بررسی قرار میگیرد، تعویض بخشی از صفحه سایش کلیه ی پره ها است. شکل 4 ناحیه سایش و محل قسمتی که قرار است تعویضشود را نشان میدهد. این تعمیر به مراحل زیر نیاز دارد:
- حذف بخش 10 اینچ در 10 اینچ از صفحات سایش که قرار است تعویض شود با استفاده از گوجینگ. اطمینان حاصل کنید که مقدار مواد مشابهی از هر صفحه سایش بهدقت علامتگذاری و حذف شود تا از بروز مشکلات نابالانسی جدی هنگام راهاندازی مجدد فن جلوگیری شود.
- صیقل دادن نواحی ساییدهشده زیرین پره ها.
- با استفاده از WPS تهیه شده، تعمیرات لازم در نواحی ساییدهشده تیغه سازنده انجام شود.
- سطح جوشکاری شده تیغه را صاف کرده و همسطح با سطح اصلی تیغه کنید و یک بازرسی 100 درصدی ذرات مغناطیسی از ناحیه جوش انجام دهید.
- صفحه سایش پوششدار کاربید کروم تعویضی را در محل قرار دهید و فضای ریشه کافی را برای اتصال خوب جوش بین تیغه سازنده و بخش فلزی پایه صفحه کامپوزیتی باقی بگذارید. مجدداً، قرار دادن دقیق قطعات پیشبرش خورده به همان اندازه کمک خواهد کرد تا لرزش هنگام راهاندازی مجدد فن کاهش یابد.
- با استفاده از WPS مربوطه، جوش اتصال صفحه سایش تعویضی به هر دو ساختار زیرین و صفحه سایش اطراف را کامل کنید. آزمایش غیرمخرب ممکن است هنگامی که لایه جوش کامل شد انجام شود، اما پس از اعمال سطح سخت نهایی مؤثر نخواهد بود.
- در نهایت یک بازرسی نهایی بصری برای بررسی یکنواختی بین قطعات قدیمی و جدید، ترکهای ناشی از تنشهای بزرگ و ظاهر کلی انجام دهید.
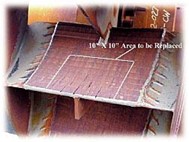
شکل 4